The first time I heard this question, I thought it would be crazy and not befitting of a professional metal fabricator. What if you just want to cut a few metal sheets accepting whatever cut quality is achievable? I did my homework and found quite a lot to inform you.
A MIG welder can be used as a plasma cutter. You’ll need an air compressor and carbon electrode in place of wire along with a number of small items. Keep the amperage between 25 and 50 and increase the wire feed speed. Avoid CO2 and choose air or nitrogen.
In this article, I’ll explore the basics and areas where you must disregard some of the requirements from regular MIG welding or any arc welding method. Here we go.
Read This Before You Start:
As you’ll cut and NOT weld, a plasma cutter is by far the most desirable option. Then, why would you use a MIG welder in the first place? The answer should be like these:
- The job doesn’t involve tons of cuts, and there is room for compromise on the quality of the cuts.
- You just don’t deem it necessary to spend time in acquiring the particular skills.
- You don’t want to bother about a considerable investment which a plasma cutter setup requires.
It is not unusual to have other reasons, but the above points come before anything else when you see it appropriate to choose a MIG welding machine over a plasma system for cutting metals.
What Does It Mean to Use a MIG Welder for Cutting Material?
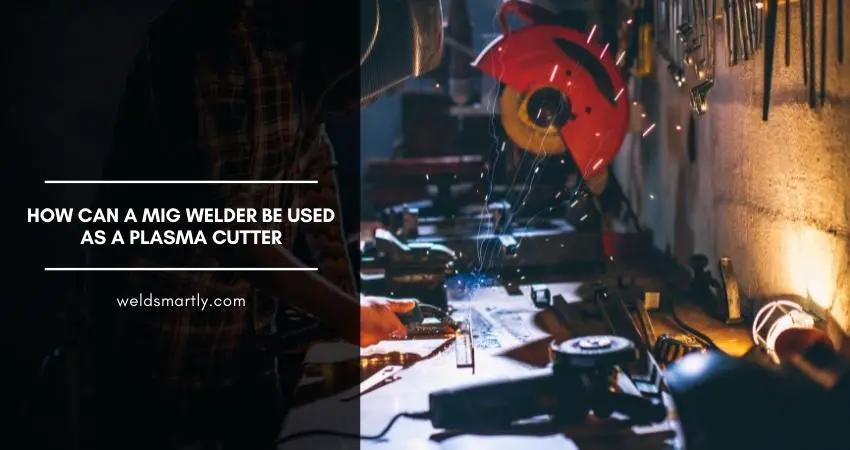
Let me give you a quick note on plasma cutting at first. As long as we’re talking about electrically conductive metal, the use of a plasma cutter remains relevant. An accelerated jet of plasma is created to cut through materials. With the passing of a gas at an extremely high speed through the constricted opening of a torch, the plasma gets formed creating an electric arc in the process.
That arc and plasma gas are utilized by the machine to make clean and precise cuts. Shop air works well for entry-level machines, but as you go upwards in terms of specs and power, pressurized gases come handy. In that case, you want argon, nitrogen, or a mixture of these gases.
A MIG welder produces an electrical arc between a work piece and a consumable electrode. The arc heats the metal pieces in a way that they start melting. Thus, joints are created, and you get the weld. MIG welding relies on shielding gases too. The gas is fed right through the MIG gun. Its job is to protect the molten metal from various atmospheric contaminants.
The feeding rate and the choice of a shielding gas are critical to the overall effectiveness of the process. The melting process may not go as expected if you fail to set both of them correctly.
One of the key differences between welding and plasma cutting is the generation of heat during the processes. A MIG welder is not known for producing as much heat as a plasma cutter does.
So, whatever you can achieve with a MIG welding WON’T be technically plasma cuts. The electrical arc created by the welder is somewhat close to a plasma minus the presence of the tremendous heat.
A Few More Insights
The inside portion of a metal stays hot when you use a MIG welder. On the contrary, the inside part remains cool during a plasma cutting process. There are more downsides to using a MIG welder for this rather unconventional task.
A plasma cutter works at least ten times faster and uses more voltage than a MIG welder to make cuts without much dross. If the speed slows off due to any reason, you might see the deposition of porous debris which is thick as well. It results in a tainted edge which requires some post-cleaning time.
Material thickness is another considerable point when comparing welding to plasma for a cutting job. Both thick and thin metals can be cut with great efficiency using a plasma cutter. But a MIG welder with all its power and technical excellence is ideal for cutting metals, not thicker than 1/2 inch.
Sometimes, you could have some luck with thicker metal, but that is nothing compared to what a high-definition or CNC plasma system can do. I guess you might be interested in this reality.
But at the same time, you can proceed with MIG welding given that you are ready to follow a few rules and techniques for optimal performance, and more importantly, a safe cutting operation. Enough of the expectations and warnings! Don’t you think? So, how can a MIG welder be used as a plasma cutter? Let’s go straight to the procedure now.
Getting Ready for Using a MIG Welder As a Plasma Cutter
As with any welding or cutting method, you need certain items to ensure your own safety and efficiency while on the job. Most of the required tools should be available at your workshop.
Gather the Safety Gear
You’re about to cut metals, but you’ll still be using a welding machine. It means you’ve got to be cautious and ready to deal with the various hazards that welding involves. You should have the right protective outfit in place, and of course, each of those items needs to be from your welding gear. So, I’m putting down a list of the essentials here in case you might want to know.
- Welding Gloves that can protect your hands from extreme heat (9,900 °F or 5,500 °C)
- Welding Helmet with UV protection dialed to 11/12
- Work Boots made of non-flammable material
- Clothing with Long Sleeves (Leather or Denim)
Gather the Required Tools
Apart from a MIG welding unit, you need some special supplies. Also, we’re talking about a small job that doesn’t involve a lot of hard work except caution. Look at the list now.
- Air Compressor
- Carbon Electrode
- Copper Tubing
- Drill
- Brass Jet, Cap, and Plumbing Valve
- Tap and Die
- Zip Ties
Prepare the Setup
- Take the copper tube and attach a brass cap cup securely on one of its ends and a plumbing valve on another.
- Drill a small hole in that cap which will make it possible for you to run threads just like a brass carburetor jet does. The role of the plumbing valve will be to let you adjust the volume of air.
- Attach the copper tube onto the handle of your welder with the zip ties to secure it.
- Put the carbon electrode making sure that the electrode tip gets a conical shape and stays sharp.
- Flex the nozzle carefully towards that tip.
- Attach a compressor hose coupling to your plumbing valve. Choose a fast-releasing coupling for this. The coupling will be required for the air compressor.
Prepare Your Metal Pieces
You’ll lose much of precision while doing this, but it doesn’t change the fact that the metal pieces still need to be prepped. Since you want the cut to be fairly straight, if not completely, use a piece of chalk to mark the path you want the cuts to go. Clamp the metal in place, so it doesn’t move as you cut. Clamp your grounding lead onto your metal to allow the arc to be produced.
Adjust the Amperage Settings
As a general rule of plasma cutting, 20 amps should be the lowest point for a plasma system if you don’t intend to cut metals, not thicker than 1/8 inch. Should you choose to cut thicker metal pieces, you must add 10 amps of power for every 1/8 inch of cut in excess.
For example, 40 and 50 amps should be adequate for 3/8-inch and 1/2-inch pieces respectively. However, this very idea could work well but not under all circumstances. Welding machines with amperage set at 25-50 generate an arc that is sufficiently hot and capable of creative oxidation in excess to blow through metal plates with a standard thickness. So, take this as a clue to start with.
Adjust the Wire Feed Speed
I didn’t tell you anything about the use of a welding wire, did I? You need to know a thing or two about the feed speed because it controls the amperage and weld penetration. But we’ll go beyond the recommended speed settings in this case since we’re cutting. Increase the speed to make it high enough to ensure that the metal gets burned through. You might find it pretty strange, but it is necessary.
Start Cutting
If your metal pieces are not thicker than 1/4 inch, you can try cutting all the way through them in one go. For thicker metal pieces, you may not be able to cut entirely through at a time. A little improvisation is needed. Gouge a welding rod into your cut to remove the molten metal formed by the groove which is common in this process.
Be Careful About Using Carbon Dioxide (CO2)
I know you’ll argue that few options are as suitable as CO2. You are right because it is a very useful reactive gas that requires no inert gas and is usable in its purest form. Well, I got a few words. CO2 is not a good choice for people engaged in commercial plasma cutting. This gas cannot be ionized easily, and more importantly, maintaining conductivity or ionization becomes a tough gig.
So, I would suggest that you exclude the CO2 input from the process and include compressed air which is a less expensive option too. You can mix nitrogen with air for a change.
Final Thought
Most people, or at least the ones I know, didn’t quite get the above process right at first. Don’t be disappointed right away, amigo. Several attempts and observations from mistakes each time will help you excel in it, should it be one of your pursuits every now and then.
With time and experience, you might as well be able to cut holes in the pieces besides cutting a straight line. Don’t move the welding rod along your cut line. Instead, keep it digging into the metal being cut. After reaching fully through your work piece, you should pass the welding rod around the hole to widen it up to a desired measurement.
Congratulations! You’ve just learned a new method to save yourself the trouble of buying a plasma setup while still being able to cut metals with your existing MIG welder. Got more questions or ideas in your busy head? Pass some of that to me while you can. Always happy to help!
Similar Articles: