Are you new to welding and wondering what polarity in welding means? Polarity refers to the direction of the electrical current flowing from the welding machine to the electrode. Understanding polarity is crucial for welders as it directly impacts the quality and strength of the weld. If you choose the wrong polarity, problems can arise, like poor penetration, weak welds, and excessive spatter.
There are two types of polarity in welding, straight polarity and reverse polarity. Straight polarity, also known as DC electrode negative (DCEN), occurs when the electrode is connected to the negative terminal of the welding machine. Reverse polarity, also known as DC electrode positive (DCEP), occurs when the electrode is connected to the positive terminal of the welding machine. Different types of welding require different polarities to achieve the best results.
In this article, we’ll dive deeper into polarity in welding and explain how it affects the welding process and the quality of the weld. We’ll also discuss the different types of polarity and when to use each one. So, whether you’re a beginner or an experienced welder, keep reading to learn more about polarity in welding.
Understanding Polarity in Welding
If you’re new to welding, you may have heard the term “polarity” being thrown around. But what exactly does it mean, and why is it important? In this section, we’ll explore the different types of polarity and how they impact the welding process.
Types of Polarity
There are two main types of polarity when it comes to welding: straight polarity (also known as electrode negative, or DCEN) and reverse polarity (also known as electrode positive, or DCEP). In straight polarity, the electrode is connected to the negative terminal of the welding machine, while in reverse polarity, the electrode is connected to the positive terminal.
In addition to these two types of polarity, there are also two types of current that can be used in welding: alternating current (AC) and direct current (DC). AC current switches direction periodically, while DC current flows in one direction only.
Impact of Polarity on Welding Process
So, why does polarity matter in welding? Well, the type of polarity you use can have a significant impact on the welding process. For example, straight polarity is typically used for welding thinner materials, while reverse polarity is better suited for thicker materials. This is because reverse polarity produces a hotter, more focused arc that can penetrate deeper into the metal.
In addition to affecting the penetration of the weld, polarity can also impact the stability of the arc. For example, AC current is generally more difficult to control than DC current, which can make it more challenging to maintain a stable arc.
It’s worth noting that the type of polarity you use will also impact the type of electrode you should select. For example, electrodes designed for use with reverse polarity will typically have a larger diameter than those designed for use with straight polarity.
Welding Current and Heat Distribution
When it comes to welding, heat distribution is a critical factor that can impact the final quality of the weld. The welding current plays a vital role in determining the heat distribution in the welding process. In this section, we will explore the role of amperage and the influence of polarity on heat distribution.
Role of Amperage
Amperage is the measure of the strength of the welding current. It determines the amount of heat generated by the welding arc. The higher the amperage, the more heat is generated, and the deeper the fusion into the base metal. However, too much heat can lead to burn-through, while too little heat can result in a weak weld.
Influence of Polarity on Heat
Polarity refers to the direction of current flow in the welding circuit. It can have a significant effect on the heat distribution during welding. In DC welding, there are two types of polarity: direct current electrode positive (DCEP) and direct current electrode negative (DCEN).
When using DCEP, the electrode is positive, and the workpiece is negative. This polarity results in more heat being generated at the electrode, which can cause faster electrode melting and a narrower bead. On the other hand, when using DCEN, the electrode is negative, and the workpiece is positive. This polarity results in more heat being generated in the workpiece, which can lead to a wider bead and better penetration.
In AC welding, the polarity changes rapidly, which can result in a more even heat distribution. However, AC welding is generally more difficult to control and requires more skill than DC welding.
Electrodes and Polarity
When it comes to welding, choosing the right electrode is crucial. But did you know that the polarity of the electrode can also have a significant impact on the quality and strength of the weld? In this section, we’ll take a closer look at electrode selection and the two types of polarity in welding.
Electrode Selection
There are many different types of welding electrodes, each with their own unique properties and characteristics. When selecting an electrode, it’s important to consider factors such as the type of metal being welded, the welding process being used, and the desired weld characteristics.
Direct Current Electrode Positive (DCEP)
Direct Current Electrode Positive (DCEP) is also known as “reverse polarity.” In DCEP, the electrode is connected to the positive terminal of the welding machine, and the workpiece is connected to the negative terminal. This polarity is commonly used for welding thicker materials, as it results in deeper penetration and faster welding speeds.
Direct Current Electrode Negative (DCEN)
Direct Current Electrode Negative (DCEN) is also known as “straight polarity.” In DCEN, the electrode is connected to the negative terminal of the welding machine, and the workpiece is connected to the positive terminal. This polarity is commonly used for welding thinner materials, as it results in less penetration and a more stable arc.
When selecting the polarity for your welding project, it’s important to consider factors such as the thickness of the material, the desired weld characteristics, and the type of electrode being used. By choosing the right polarity and electrode, you can ensure a strong, high-quality weld that meets your needs.
Materials and Polarity Choices
When it comes to welding, choosing the right polarity is essential for achieving the desired results. The choice of polarity depends on several factors, including material thickness, the type of material being welded, and the welding position. Here are some important considerations to keep in mind when selecting polarity for different metals.
Polarity for Different Metals
For ferrous metals, such as steel, it’s generally best to use direct current electrode negative (DCEN) polarity. This polarity setting allows for deeper penetration and better control of the weld pool. On the other hand, when welding non-ferrous metals like copper or aluminum, alternating current (AC) polarity is often used. AC polarity is ideal for non-ferrous metals because it helps to prevent oxide buildup on the surface of the metal.
Effects on Material Thickness
When welding thin materials, it’s important to choose the right polarity to avoid burning through the material. For thinner materials, DCEN polarity is often recommended because it produces a narrower and more focused arc, which can help prevent burn-through. In contrast, DCEP polarity is often used for thicker materials because it produces a wider and more stable arc, which can help to achieve better penetration.
It’s also important to consider the type of material being welded when selecting polarity. For example, when welding stainless steel, it’s generally recommended to use DCEN polarity to achieve a deeper and more controlled weld. However, when welding mild steel, DCEP polarity is often used to achieve a wider and more stable arc.
Welding Techniques and Polarity
When it comes to welding, polarity plays an important role in determining the quality and strength of the weld. The wrong polarity can lead to problems such as poor penetration, weak fusion, and excessive spatter. In this section, we’ll discuss the different welding techniques and their polarity considerations.
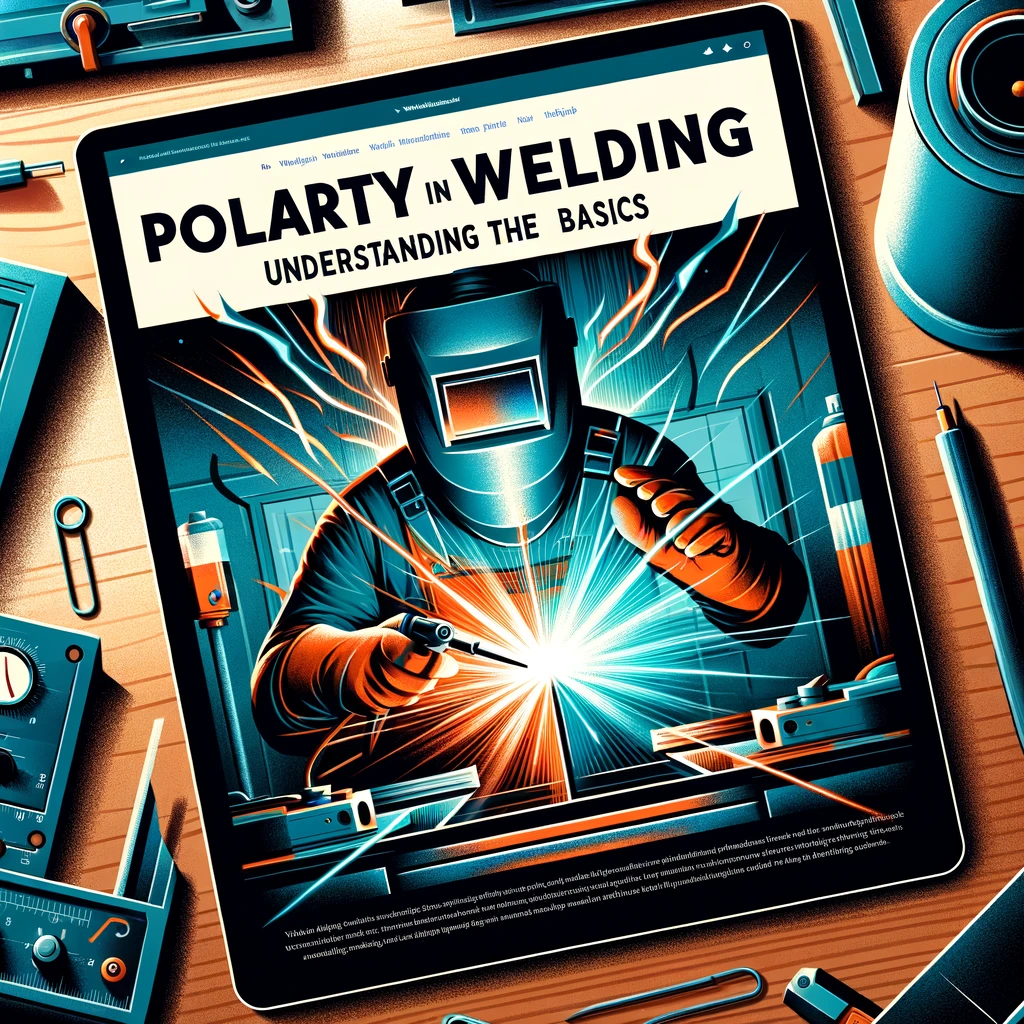
SMAW and Polarity
Shielded Metal Arc Welding (SMAW) is a welding technique that uses a consumable electrode coated in flux to lay the weld. The polarity used in SMAW depends on the type of electrode being used. For example, if you’re using an electrode with a high cellulose sodium coating, you’ll need to use reverse polarity (DC electrode positive). This polarity allows for deep penetration and fast travel speeds.
On the other hand, if you’re using an electrode with a low hydrogen coating, you’ll need to use straight polarity (DC electrode negative). This polarity provides better control over the weld puddle and produces a cleaner weld.
TIG and Polarity
Gas Tungsten Arc Welding (TIG) uses a non-consumable tungsten electrode to create the weld. The polarity used in TIG welding is typically straight polarity (DC electrode negative). This polarity allows for better control over the weld puddle and produces a cleaner weld. However, some TIG welders prefer to use alternating current (AC) polarity, which allows for better heat distribution and reduces the risk of arc blow.
MIG and FCAW Polarity Considerations
Gas Metal Arc Welding (MIG) and Flux-Cored Arc Welding (FCAW) are both wire-feed welding techniques that use a consumable electrode to lay the weld. The polarity used in MIG and FCAW depends on the type of wire being used. For example, if you’re using a wire with a positive polarity (DC electrode positive), you’ll need to use reverse polarity. This polarity provides better penetration and faster travel speeds.
On the other hand, if you’re using a wire with a negative polarity (DC electrode negative), you’ll need to use straight polarity. This polarity produces a cleaner weld and reduces the risk of spatter.
Choosing the Right Polarity for the Job
When it comes to welding, choosing the right polarity is crucial. It can affect the weld penetration, weld quality, and welding performance. Here are some tips to help you choose the right polarity for the job.
Factors Influencing Polarity Selection
There are several factors to consider when selecting polarity, including the type of material being welded, the thickness of the material, and the type of electrode being used.
For example, when welding aluminum or magnesium, it is best to use reverse polarity (DC electrode positive) because of their low melting point. On the other hand, stainless steel and titanium respond better to alternating current polarity.
Practical Tips for Polarity Adjustment
Adjusting the polarity of your welding machine is a simple process. Here are some practical tips to help you adjust the polarity for your welding job:
- Refer to the manufacturer’s recommendations for the correct polarity for the type of material and electrode being used.
- Test the weld on a scrap piece of material to ensure the polarity is correct before welding on the actual project.
- Adjust the polarity by switching the cables on the welding machine. For example, to switch from DC electrode positive to DC electrode negative, switch the electrode cable with the work cable.
- Monitor the weld penetration and quality to ensure the correct polarity is being used.
By following these tips, you can ensure that you are using the correct polarity for your welding job, resulting in high-quality welds and optimal welding performance.
Advanced Considerations in Welding Polarity
When it comes to welding, polarity is a critical factor to consider. The direction of current flow in an electrical circuit affects the properties of the weld, including heat direction and weld strength. In this section, we’ll discuss some advanced considerations in welding polarity and how they can impact your welding projects.
AC vs. DC in Specialized Welding
While most welding projects use direct current (DC) polarity, there are some specialized welding techniques that require alternating current (AC). AC welding is typically used for welding aluminum and other non-ferrous metals, as well as for some specialized welding techniques like plasma cutting and TIG welding.
AC welding involves the current alternating between positive and negative polarity many times per second at a rate known as frequency. This can create challenges with arc stability and spatter, which we’ll discuss in the next subsection.
Managing Arc Stability and Spatter
One of the biggest challenges with welding is maintaining arc stability while minimizing spatter. Arc stability refers to the consistency of the welding arc, while spatter refers to the bits of molten metal that can fly off during welding.
Arc stability and spatter are closely related to polarity, as well as other factors like electrode type, power source, and shielding gas. For example, DC electrode positive (DCEP) polarity is known for producing less spatter and a more stable arc, while DC electrode negative (DCEN) polarity is known for producing more spatter and a less stable arc.
To manage arc stability and spatter, it’s important to choose the right polarity for your welding project, as well as the right electrode type, power source, and shielding gas. Other factors that can impact arc stability and spatter include arc blow, which refers to the tendency of the welding arc to be deflected by magnetic fields, and an unstable arc, which can occur when the welding arc is too long or too short.
Welding Safety and Polarity
When it comes to welding, safety should always be a top priority. This includes understanding the importance of polarity in welding. By knowing how to handle welding equipment and power supply, you can help ensure a safe and effective welding experience.
Electrical Safety in Polarity
One of the key safety concerns when it comes to polarity in welding is electrical safety. Welding machines and power sources can pose a serious risk of electrical shock if not handled properly. To avoid this risk, always follow the manufacturer’s instructions for use and maintenance of your welding equipment.
Make sure you are using the proper power supply and that it is grounded. Inspect your welding machine and power supply regularly for any signs of wear or damage. If you notice anything unusual, stop using the equipment immediately and have it inspected by a qualified professional.
Handling Equipment and Power Supply
In addition to electrical safety, it is important to properly handle your welding equipment and power supply. This includes using the correct polarity for the type of welding you are doing.
Direct current electrode positive (DCEP) is used for welding thicker materials, while direct current electrode negative (DCEN) is used for thinner materials. Alternating current (AC) is used for welding aluminum and other non-ferrous metals.
Always make sure your welding equipment and power supply are properly set up for the type of welding you are doing. This includes selecting the correct polarity and ensuring that all connections are secure.
Welding Training and Technical Knowledge
Welding is a hands-on job that requires a fair amount of technical knowledge. As a beginner, you might be wondering where to start with your training. In this section, we’ll discuss some educational resources for welders and how to build technical expertise in polarity.
Educational Resources for Welders
There are many resources available to help you build your welding skills. Whether you prefer online learning or in-person classes, there’s something for everyone. Here are a few options to consider:
- Trade schools and vocational programs: These programs offer hands-on training in welding and other trades. They typically take 6-12 months to complete and provide a solid foundation in welding techniques and safety.
- Online courses and tutorials: There are many online courses and tutorials available for free or at a low cost. These resources can help you learn welding basics and more advanced techniques.
- Books and manuals: There are many books and manuals available on welding. These resources can provide in-depth information on welding techniques, safety, and more.
Building Technical Expertise in Polarity
As you learn to weld, you’ll need to develop technical expertise in polarity. Polarity refers to the direction of current flow in an electric circuit. In welding, polarity determines which part of the welding circuit carries the majority of the current and heat.
To build technical expertise in polarity, you should:
- Understand the basics of electrical circuits: To understand polarity, you need to understand the basics of electrical circuits. This includes concepts like voltage, current, resistance, and power.
- Learn about the different types of polarity: There are two types of polarity in welding: direct current electrode positive (DCEP) and direct current electrode negative (DCEN). DCEP is used for welding thicker materials, while DCEN is used for welding thinner materials.
- Practice welding with different polarity settings: As you practice welding, experiment with different polarity settings to see how they affect the quality of your welds. Keep track of your results so you can identify which settings work best for different materials and applications.
By building technical expertise in polarity, you’ll be able to produce high-quality welds that are strong and durable.
Frequently Asked Questions
What are the effects of using incorrect polarity in welding processes?
Using incorrect polarity in welding processes can lead to several issues. For instance, it can cause poor penetration, excessive spatter, and weak welds. The polarity of the electrode in relation to the workpiece affects the heat distribution and the depth of penetration. Therefore, using the wrong polarity can result in a weak and brittle weld, which can compromise the structural integrity of the welded joint.
How can you determine the correct polarity setting for different welding applications?
The correct polarity setting for different welding applications depends on several factors, including the type of electrode, the material being welded, and the welding process being used. Generally, DC electrode negative (DCEN) is used for welding thin materials, while DC electrode positive (DCEP) is used for welding thicker materials. It is essential to consult the manufacturer’s recommendations and welding charts to determine the correct polarity setting for a specific welding application.
Can you explain the differences between straight polarity and reverse polarity in arc welding?
Straight polarity, also known as DC electrode negative (DCEN), is when the electrode is negative, and the workpiece is positive. Reverse polarity, also called DC electrode positive (DCEP), is when the electrode is positive, and the workpiece is negative. The choice of polarity affects the welding process’s stability, spatter, and penetration. In general, straight polarity provides deeper penetration, while reverse polarity produces a wider and flatter bead.
What are the implications of electrode polarity on weld penetration and quality?
The electrode polarity affects the weld penetration and quality significantly. DC electrode negative (DCEN) provides deeper penetration, while DC electrode positive (DCEP) produces a wider and flatter bead. The choice of polarity also affects the heat distribution and the arc stability, which can impact the weld quality. It is essential to choose the correct polarity setting based on the material being welded and the welding process being used.
How does the choice of polarity affect the deposition rate and bead appearance in welding?
The choice of polarity affects the deposition rate and bead appearance in welding. DC electrode negative (DCEN) produces a narrow and deep penetration, while DC electrode positive (DCEP) produces a wider and shallower penetration. The deposition rate is higher with straight polarity, while reverse polarity produces a wider and flatter bead. The choice of polarity depends on the material being welded, the welding process being used, and the desired weld quality.
In stick welding, which is preferable: electrode positive or electrode negative, and why?
In stick welding, the choice of polarity depends on the type of electrode being used. Generally, DC electrode negative (DCEN) is used for welding thin materials, while DC electrode positive (DCEP) is used for welding thicker materials. The electrode polarity affects the heat distribution, penetration, and arc stability, which can impact the weld quality. Therefore, it is essential to choose the correct polarity setting based on the material being welded and the welding process being used.