Plasma cutting is a cost-effective cutting method. Laser cutting offers clean and smooth cuts with complex patterns or shapes. Waterjet brings versatility and precision. It is as simple as I can keep it if you ask me why you should choose one and disregard the rest in the first place.
Well, all of these mechanisms are useful. Which one do you think will help you the most on your next project? I think it is hard to answer for there’re chances to ignore the better one by mistake and end up doing more only to get less.
I’ve spent hours and days to find out the truth, and in this article, I’m going to share everything I learned about them, so you can get to the bottom of each process and choose with the required information at your disposal.
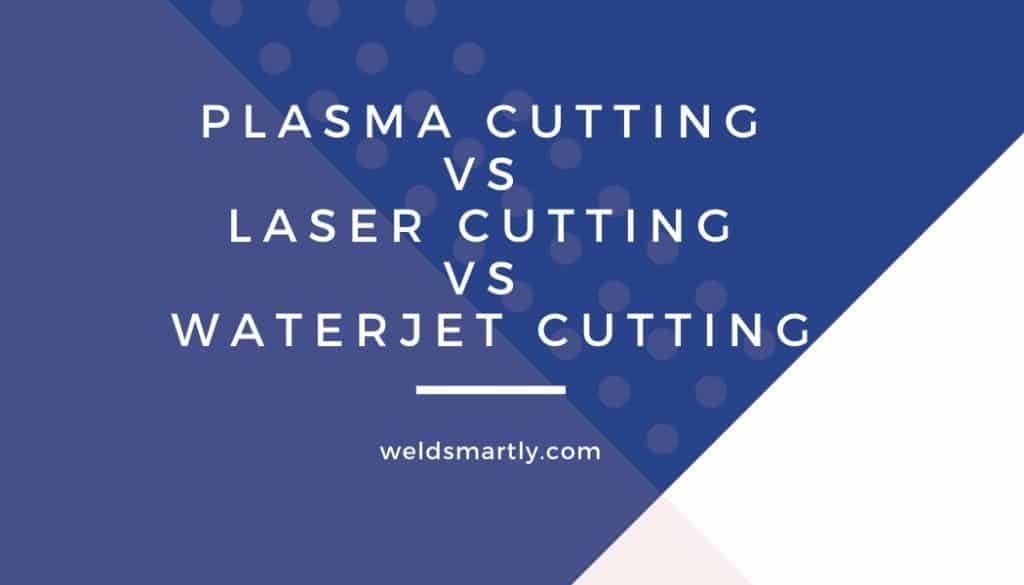
Overview of Each Process
Each of these cutting operations is popular and has retained their appeals over the past few decades. So, you cannot just tell that one of them is better than others without putting the due diligence to learn how they work and what you can or cannot expect from them.
Plasma Cutting: Definition and Mechanism
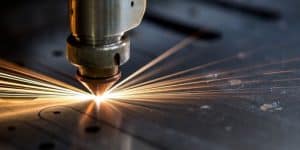
People in general including those with little to no idea about metal cutting fabrication have a common idea about the three states of matter such as the solid, the liquid, and the gaseous form. Energy plays a role in the change of matter from one state to another which goes like this:
A solid with a certain kind of energy (heat) being applied becomes a liquid which also becomes a gas (steam) with the increase of heat. Any further increase of heat being applied to the steam results in a special state known as plasma where that steam becomes electrically conductive and ionized.
The appliance we need to use to create this state is a plasma cutter that uses the ionized gas to make the transfer of energy from a standard power supply to a conductive metal. Why do we call this a cutting process?
It is actually a melting process that requires the formation of a plasma arc which begins as argon, nitrogen, oxygen, or shop air gets pushed through a nozzle orifice located inside the plasma torch. The gas flow gains a high pressure. An electric arc from an external power supply meets that gas flow to create a plasma jet that contains ionized gas.
In a matter of seconds, the jet gains temperatures from 20,000 – 40,000° F and quickly melt/pierces through the metal work piece and expel the molten material from that cut. The introduction of this method became relevant when it was found to produce faster and cleaner cuts than oxyfuel.
Additional Read: History of Plasma Cutting Technology
Advantages and Applications
By comparing plasma cutting to oxyfuel in terms of speed and cut quality, I didn’t indicate that its usability is limited to its better productivity than oxyfuel’s. Following is the list of benefits why this cutting method has been so popular.
- You can cut more parts while taking less time. You may choose to cut material that is 0.25-inch thick. Again, the material can be as thick as 2 inches. Nevertheless, you’ll get better speed (12x and 2x faster than with oxyfuel respectively) which helps increase productivity.
- Chemical reactions might occur between the work piece and the gas in use resulting in oxide slug or dross. Modern plasma cutters use electrically charged gas flow at high temperatures to blow away that molten metal and eliminate the need for consistently grinding or chiseling, a typical activity in oxyfuel cutting.
- Applications that require piercing from inside can be tackled efficiently. While oxyfuel takes more than 30 seconds to pierce metal that is 0.50-inch thick, a plasma cutter is equipped to do the same in just two seconds.
- Warping is a common issue as you cut materials as thin as 0.25 inch. Fast cutting speed and automatic control of heat being transferred to the work piece are some of the great things about a plasma cutter, which dramatically keep warping to a minimum.
- Besides bringing automation to your work, plasma cutting is applicable to any material that is electrically conductive including aluminum, high-alloy, and structural steel. It also allows you to process excellent blanks for sheet metals.
- To improve plasma cutting even to a greater extent, you can use a CNC machine that allows you to repeat the process with great precision.
From DIY/hobbyist shops to large industrial sites, plasma cutting has become a popular choice for its precision and speed with affordability. Whether you work at an automotive repair or restoration shop, or a metal fabrication workshop, this method can be useful. We see its uses in some industrial construction sites or salvaging/scrapping workshops too.
Disadvantages and Limitations
Despite the positive aspects of the operation, you’ll experience the following drawbacks while using a plasma cutter.
- It is ideal for material thickness up to 120 mm for cutting underwater and 180 mm for dry cutting
- You cannot avoid making a wider kerf on most occasions.
- High power consumption is almost unavoidable.
- Generation of excessive noise, bright flashes, and fume are some of the hazards you must be prepared to survive.
- Relatively costly electrodes might affect the budget for a particular project.
Laser Cutting: Definition and Mechanism
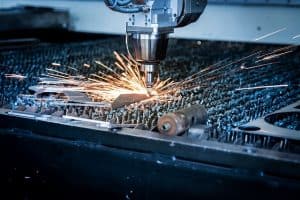
LASER stands for “Light Amplification by Stimulated Emission of Radiation”. When you laser cut something, it means you use a thermal-based fabrication method where a laser beam is applied to cut and/or etch materials into the designs, shapes, and patterns conceptualized prior to the process.
A high-power laser is created and then guided through CNC and optics to direct the material or the beam. A motion control mechanism is typically used to follow a G-Code or CNC code of the intended pattern that you want to cut onto the metal.
The laser beam burns and melts the metal. A coaxial jet of gas then ejects the molten properties and creates a kerf that can be 0.08mm to 1mm in width. You can get continuous cuts by moving a laser beam under a CNC control system.
The laser beam is thin and focused requiring non-contact machining and no custom-made tools. Where there is a need for cutting intricate parts from materials like ceramics, gemstone, silicon, wood, glass, plastic, non-metals, and paper, you can rely on this process.
Metals that can be cut include brass, steel, nickel, and tungsten. Metals with serious light-reflective and heat-conductive properties are not ideal for this process. Copper alloys and aluminum are such metals that require more than regular lasers.
Advantages and Applications
Laser cutting is as much suitable for industrial applications as it is for artistic uses, and behind this widespread popularity are the following upsides that it offers.
- The same laser cutting setup lets you cut a wide variety of shapes and intricate patterns if the material thickness remains the same.
- With this method, you can achieve an accuracy of just 0.1 mm, give or take. Even, you need not apply any after-treatment step or add tolerances, should you have to maintain this precision.
- As long as you’re cutting several parts that need to replicate each other, you cannot ignore the appeal of +/- 0.05 mm tolerance.
- Laser cutting can be a game-changer in certain circumstances where you need complex cuts out of materials with 10 mm in thickness. Things can be done a lot faster with this process than with any traditional one.
- There is no denying the fact that automation is always a key to anyone’s choosing these thermal procedures. Laser cutting is more than just a basic iteration of this concept as some advanced machines come equipped with feeding systems and follow-up conveyors.
- With the proper setup and required expertise, you wouldn’t worry much about burr and heat affected zone which is often very small in a perfect world.
- The initial cost might overwhelm you, but the durability of a setup is certainly worth the price. The setup sees nearly zero mechanical friction because the beam and the material come into contact with each other during the operation.
- Some laser cutters allow laser marking which means you can put it to use for many other applications besides cutting.
Clean cuts with smooth finishes are why laser cutting is a familiar method in industries like aerospace, automotive, electronics, semiconductors, and medicine. The technology behind this process has gained significant developments in the modern era, which make it an advanced procedure in the surgical field, particularly in high-precision procedures as in eye surgery.
Disadvantages and Limitations
Just like any thermal process, laser cutting doesn’t come without its challenges and setbacks. Following are some of the drawbacks of the method.
- Although power consumption is subject to the very application you’re handling, laser cutting cannot be done appropriately without the use of a considerable amount of energy.
- You need a little expertise. Any mistake from your part while adjusting the settings for the temperature and the distance may not end well for the metal you’re working on. Burning and discoloration are pretty common.
- You may experience physical damages in the event of an accidental contact with the laser beam.
- The potentiality of this method is limited to certain metals and their thicknesses.
- Inconsistent production speed can be an annoying problem, especially when you need to cut various metals.
- Toxic emissions are also common as you cut plastic or similar materials.
- The edges of most materials may get burned in the process leaving you little to reverse the result.
Waterjet Cutting: Definition and Mechanism
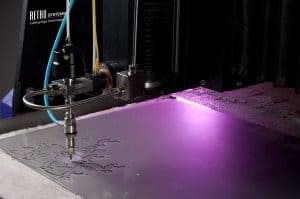
This particular process involves slicing into various materials and metals employing a high-pressure jet of water, or a mixture of an abrasive substance and water at great velocity. Sharing considerable similarity to the process of water erosion as seen in the nature, waterjet cutting comes concentrated and accelerated to a far greater degree.
A pump equipped with an ultrahigh-pressure mechanism is required to generate a high-pressure stream of water, rated up to 6,480 bar or 94,000 psi. It is up to 80 times the pressure contained in a fire hose.
A small jewel orifice is required to convert this much pressure into velocity in the form of a supersonic stream, nothing bigger than one of your hairs, to slice soft materials. So, how can we increase the cutting power? Introducing garnet to that stream is the key.
As garnet and water leave the machine’s cutting head, their exit occurs at a speed which is four times higher than that of sound. Thus, we are able to cut metals thicker than one foot.
You can use either a pure or an abrasive waterjet technology. For greater versatility in the cutting operations, some professionals combine both of these technologies, but that requires a specific set of skills.
Pure waterjet is ideal for cutting cement board, foam, gasket, insulation, carpet, food, paper, plastic, and other soft materials while abrasive waterjet is suitable for harder materials like ceramic, stone, glass, and metals.
Advantages and Applications
If there is one cutting process that doesn’t compromise or change the inherent structure of the material being cut, I would say it is the most reliable way to go. You wouldn’t worry about any interference with or alteration to the intrinsic properties of the material in use.
However, several other benefits are relevant as far as cost and material supports are concerned. Look at the list below for more benefits.
- It is a cold cutting method that results in zero heat-affected zones. Also, the hardening of material doesn’t occur.
- Part of the versatility that waterjet cutting offers is its Omni-directional flexibility. It means you can cut metals using virtually any direction.
- Much of the excellence that this procedure brings to your work is that it cuts and perforates all materials except a handful of metals without creating pockets or holes.
- It is possible to cut the final shapes or the ones very close to those without undertaking any secondary processing.
- You’ll enjoy the flexibility and minimal stress while doing machine integration, fixture deployment, and cutting.
- Dust or other harmful gases being present in a reduced quantity make the process safe and environmentally neutral.
Waterjet cutting has seen more frequent adoption in fabrication work than other fields have. Aerospace, mining, and a few other industries rely heavily on this technology for shaping, reaming, and cutting operations.
Disadvantages and Limitations
Whatever impressions the above points might have on you about waterjet cutting can be justified in the light of the many drawbacks this technology comes with. Check the following points out.
- Only a few high-end orifices are reliable while most of these components may break down sooner and disrupt the operation more frequently than expected.
- Cutting speed might not always be consistent. Oftentimes, you may experience slower operations which lead to less output.
- It is easy to lose much of the accuracy you expect to achieve. Thicker materials can hardly be cut with great precision. Also, waterjet cuts better diagonally than the “up and down” direction.
- Procurement of abrasive materials can be hard and affect the production cost.
- It is not the best process to use to make intricate cuts, engravings, or anything that requires fine details.
Well, I think you’ve had enough about these three cutting procedures. I haven’t given you a comparative overview yet, have I? There you go.
Plasma vs. Laser vs. Waterjet: A Comparative Discussion
With the basics, benefits, and limitations of each process explained, I think I can offer a full picture of efficiency and scope of these cutting technologies using several factors that matter most when you’re tackling a real-life project.
Cost of Purchase: Plasma Is the Winner
The budget you’re going to make available is always a crucial factor, no matter which type of cutting you prefer. Plasma cutters are considered the most affordable of all the machines required by these operations.
A CNC plasma cutter can be on top of the line and cost anywhere between $15,000 and $300,000 depending on the size, type, and other features. However, a standard setup would cost you $100,000. For a laser or a waterjet cutter, the CNC setup may cost you at least $100,000.
Costs of waterjet machines can be as high as $350,000. I’m talking about the most sophisticated units which come with an “Ultra high-pressure intensifier” pump.
A CNC laser machine usually comes at a high cost which is at least $300,000. You can settle for a cheaper option, but that would only offer mediocre performance. If you don’t want to compromise on anything, the price could be as high as $1,000,000.
Accuracy and Precision: Waterjet Is the Winner
You want to look at the size of the actual cut that resulted based on the programmed size of the cut. Comparative measurement of these two sizes gives you an idea about precision.
Included in this particular consideration is the kerf width, the measure of how small (the size) of an inside contour that can be cut. You need to take heat distortion into account too because this condition can compromise the size of the finished cut. It can also cause that part to warp in the process.
Considering all things, I believe waterjet should be the method you can choose for the ultimate precision. The measure is typically +/- 0.005 inch, and the kerf width can be around 0.035 inch. The best thing about Waterjet is that you need not bother about heat-distortion.
With cut part measures of +/-0.005 inch and kerf width being 0.025 inch, laser cutting comes next to the waterjet. However, you can avoid the consequences of heat distortion with this process, particularly if you’re cutting a thicker plate.
Plasma cutting is rated poorly with a typical tolerance for part sizes up to +/-0.020 inch, and kerf width of 0.150 inch. Again, heat distortion can be a big deal, but you wouldn’t face the problem that much with underwater plasma cutting.
Cut Quality: Waterjet Is the Winner
The finished edge of the cut part should be square, at least that is what anybody would expect. Cut quality indicates how perfect those square cuts can be. Associated with this is the amount of dross sticking to the cut part’s bottom.
Waterjet is known for producing cuts with pretty much of perfect square edges with no pierce spatter or dross at the bottom of the parts. Laser cutting is not very far from waterjet except for the pierce spatter and dross created while cutting thicker steel.
Many professionals want to ignore plasma cutting over the excuse that the cut quality couldn’t be good enough. In fact, that is more than an excuse because plasma produces edge bevel angles and dross. The amount can be small, but you cannot get rid of them completely. Larger kerf width is another problem that results in as much pierce spatter as you would hate to see.
Material Thickness: Plasma Is the Winner
Plasma cutting is ideal for applications where the material thickness is up to 120 mm. For the most affordable operating cost, you can pick up a machine that cuts up to 20 mm in thickness. Waterjet comes very close, but you shouldn’t cut anything that is thicker than 100 mm.
Laser cutting works best on materials having a thickness up to 40 mm. However, carbon steel needs to be under 20 mm, and stainless steel has to be below 16 mm. So, laser cutting won’t allow you to gain greater advantages over the other two methods where thickness is concerned.
Production Rate, Speed, and Operating Cost: Plasma Is the Winner
In order for you to determine how much it costs to run an operation, you must take the production rate into account. You can judge this rate by comparing it to the cutting speed. Let me present you a simple way to calculate it.
Cost Per Part = Cost Per Hour (Running the Machine) / Number of Cut Parts (Per Hour)
Let’s assume that you’ll use only one cutting tool for each of these cutting methods. Using the correct settings, a standard plasma cutter cuts up to 200 inches per minute. Compared to this number, a laser cutter cuts only up to 70 inches per minute (IPM). Waterjet goes kind of slow, and you can expect only 15 IPM.
Again, the lowest rate can be 60 IPM with a plasma cutter, 20 IPM with a laser cutter, and 5 IPM for a wide variety of thicknesses and materials. You can ramp the rate up by adding a few more tools to the setup. But that doesn’t change a plasma system’s being on top.
As operating cost comes into play, you should consider a few other factors such as power, gases, abrasive materials, consumables, routine maintenance, and other fixtures. The cost of running a plasma operation is lower than the other two methods.
Without going very deep into the breakdown of costs, I would say you can do plasma cutting at $15 per hour whereas the laser cutting operations would cost $20 per hour, and waterjet may cost up to $30 per hour or even higher.
Final Words
Now that I’m about to bring this discussion to an end, you would prefer having my concluding remarks on all three processes to reading all that I’ve told over and over again.
Should you always need to choose production rates as well as affordability over other factors, plasma cutting beats the other two by a clear margin. Whether you run a small shop or part of a large-scale operation, you cannot put this very factor out of the equation.
Some people are more into detailing than into merely cutting something. Laser cutting is often viewed as the job better handled by people with the need and skills for delicate work. Plasma cutting can be a good choice but not certainly as favorable as the laser.
When your project involves several materials including both soft and hard ones, waterjet gives you the ultimate advantages. Laser cutting proves useful only if you wouldn’t have anything other than some plastics, metals, fiberglass, and fabrics. A plasma cutter works wonder on conductive metals, especially aluminum, mild and stainless steel. So, waterjet cutting offers flexibility like no other processes.
I hope this entire article has enlightened you as to the debate among these three popular power cutting methods. Feel free to ask even more questions as you have. I only wish you would have good luck with the next project.