The cost or availability of argon is not why you must know how long it lasts. TIG welding without an inert gas like argon is not recommended in a perfect world. Again, you would hate to stop in the middle of a project just because the existing amount of argon is not sufficient. That is why, you want to know how long to expect the gas to be available before a project gets underway.
An argon cylinder that contains 125 cubic feet (CF) of the gas lasts up to 5 hours at a flow rate (CFH) of 25. Mathematically, the duration is the result of the cylinder capacity divided by the flow rate. Besides CFH being the key, other factors also affect the duration.
In this article, I’ll cover everything that explains why argon lasts for the count of hours I specified above and how you can maximize its potential in terms of continuity without compromising the quality of your welding work. Let’s get down to details.
Argon Tank Sizes and Flow Rates
The amount of argon that is released per hour is the flow rate which is extremely important for anyone who wants to calculate the time a gas container may last while being used for TIG welding. The term used for this purpose is ‘Cubic Feet per Hour’ or ‘CFH’.
The simplest way to find out how long your particular cylinder should last is to divide the capacity of the cylinder by the flow rate. Now, I think I should fill you in on an argon cylinder/tank, so you can have a rough idea.
Argon cylinders come in eight different sizes which also determine the capacity of the containers. Each size is represented by a number (two or three digits) or letter(s).
Cylinder Name | Capacity in Cubic Feet |
R or 20 | 21 |
RR or 40 | 40 |
Q1 or 60 | 65 |
Q or 80 | 83 |
S or 125 | 125 |
S or 150 | 155 |
K or 250 | 251 |
T or 330 | 335 |
Assuming that you’re using an S or 150 cylinder that contains 155 cubic feet of argon, I would say you can weld up to 6 hours at 25 CFH. The bigger the capacity of the container is; the longer argon lasts. Also, the lower the CFH is; the longer the cylinder serves.
That seems too easy, right? I guess you wouldn’t read an entire article if the calculation was so simple. The flow rate I used to find a result is just a regular assumption. A typical TIG welding project requires the flow rate to be between 10 CFH and 35 CFH and sometimes higher.
What if you need to increase or decrease the rate? Well, this question brings another quick discussion into our consideration. You shouldn’t decrease or increase the CFH without knowing how a chosen rate is going to serve you in the first place. Otherwise, you’ll only lose the valuable argon longer than expected.
As argon exits a welding nozzle, its density and velocity differ from those of whatever atmospheric gases are available in the surroundings. These differences can lead to the formation of currents which may cause the argon flow that is already formed to turn from a laminar state to a turbulent one.
An increased flow rate can potentially make the laminar flow more turbulent. The problem, in this case, is that a turbulent state of gas flow makes it likely for the weld to get contaminated. A decreased rate, if not too much, causes the flow to become less turbulent and more laminar, and thereby very little room for contamination.
As alarming as it sounds to use a high flow rate, too low CFH can also be less desirable than you think. If the velocity of the atmospheric gases is too much for the flow rate of argon, the gas column can be potentially broken down or at least compromised enough to cause contamination of the weld.
So, what exactly makes life easier for you while choosing between increasing and decreasing CFH? You’ll have a definitive answer later in this article, but at this point, I think you should understand another factor.
Gas Pressure
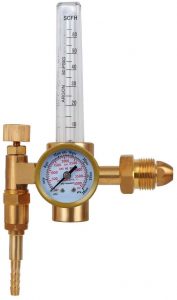
Welding professionals are more attentive to adjust the flow rate than the pressure which is measured in ‘pounds per square inch’ or ‘PSI’. Despite this, you need a basic idea about the correct amount of pressure which can be anywhere between 20 PSI and 30 PSI for 35 CFH to 50 CFH. Remember adjusting the PSI only after deciding on the CFH.
As promised, I’ll discuss the essential matters to clear the confusion regarding CFH settings. You need to look at the consumables you are about to use.
Collet Body and Gas Lens
Consumables for TIG welding come with a collet and a nozzle paired with a collet or a gas lens body. A collet body works well for normal applications while a gas lens body is ideal for critical applications.
With a collet body, argon can either spiral or become excessively turbulent while exiting your nozzle. But you can avoid this unfavorable outcome by preventing the tungsten from extending out of the nozzle any further than the nozzle’s inside diameter. On the contrary, a gas lens body is designed to reduce turbulence and increase the coverage of argon.
Here comes the flow rate again which actually has a lot to do with a gas lens or a standard collet body. The material you’re welding, the diameter of electrodes, and the size of the nozzle (cup) are relevant too. Don’t worry just yet. I’m presenting you a quick chart to help you with the CFH settings.
Electrode Diameter (Inches) | Cup/Nozzle Size | CFH for Collet Body | CFH for Gas Lens |
0.020 | 3, 4, 5 | 5 – 8 | 5 – 8 |
0.040 | 4, 5 | 5 – 10 | 5 – 8 |
1/16 | 4, 5, 6 | 7 – 12 | 5 – 10 |
3/32 | 6, 7, 8 | 10 – 15 | 8 – 10 |
1/8 | 7, 8, 10 | 10 – 18 | 8 – 12 |
5/32 | 8 or 10 | 15 – 25 | 10 – 15 |
3/16 | 8 or 10 | 20 – 35 | 12 – 25 |
1/4 | 10 | 25 – 50 | 20 – 35 |
Note: The above settings are recommended when you weld alloy, stainless, or carbon steel, or other ferrous metals. TIG welding aluminum may require variable CFH settings.
So, you’ve seen why I couldn’t offer you a straight answer before you know why the CFH settings may vary and affect the serviceability of an argon tank with regards to duration. I know I’ve already said too much, but my friend, you cannot benefit from my words without a little more on the topic.
Does the Wire Feed Speed Matter?
The speed of your wire feed determines the travel speed or the size of your weld profile. Increased feed speed requires higher CFH for proper coverage. So yes, the speed of the wire feed matters.
How Can You Ensure That Argon Lasts Long Enough?
This section involves two specific factors such as post-flow and pre-flow of argon which is more associated with weld quality than with the hours argon lasts for. But proper uses of these features help you ensure high-quality welds using just enough of argon, not losing it unnecessarily.
Keep the pre-flow of argon for at least 0.2 seconds. Making it slightly longer is okay too. You need to have at least eight seconds of post-flow operation. You can find out the amperage setting at which you want to weld and divide the amps by ten. The result is the minimum duration in seconds the post-flow needs to continue.
Whether you increase or decrease the span of pre-flow or post-flow, the action affects the use of argon, if not much. Maybe, I’ve made my points. But as I would like you to get something that can guide you through real-life situations, I’ll end this articles with two useful notes.
Wrapping Up
Flow rate is the key, isn’t it? You also know how beneficial it could be to have a laminar flow and avoid any kind of turbulence. So, try to use lower numbers for the CFH if the atmosphere is not very windy.
Under a regular condition, use a regulator flowmeter that allows you to regulate the CFH and gives you accurate readings of the flow at a given time. For outdoor applications where wind and other elements are involved, you can get a flowgauge regulator which is a more durable yet cheaper option.
You got everything I intended to offer through this article. Feel free to ask more. Safe welding!